Spritzguss bietet die optimale Möglichkeit zur Skalierung der Produktion. Vor allem für die Großserienproduktion geeignet, können Sie den Prozess durch die Materialwahl der Spritzgussform an deine Produktionsbedürfnisse anpassen. So kann sich das Verfahren schon ab einer Kleinserie von 100 Teilen lohnen. Auf den ersten Blick erscheint dabei alles ganz einfach. Allerdings gibt es Spritzguss Design Hinweise, die Sie beim Entwerfen Ihrer Teile beachten sollten.
Passendes Material
Verschiedene Materialien können für den Spritzguss verwendet werden, mit jeweils verschiedenen Eigenschaften. Ein wichtiger Spritzguss Design Hinweis ist die Entscheidung, welches Material Ihren Anforderungen entspricht.
Für das Spritzgussverfahren eignen sich unter anderem Polypropylen (PP), Polyethylen (PE), ABS oder Nylon (PA). Polypropylen ist einer der meist verwendeten Spritzgusskunststoffe, der häufig für Verpackungen eingesetzt wird. Es lässt sich schweißen und hat eine sehr gute chemische Beständigkeit.
Eine hohe chemische Beständigkeit weist auch Polyethylen (PE) auf. PE ist neben Polypropylen der gebräuchlichste Kunststoff und wird ebenfalls für Verpackungen und Folien verwendet, kommt aber auch häufiger für Rohre oder Kabelisolationen zum Einsatz. Polyethylen ist leicht, elastisch und weist eine hohe Schlagfestigkeit auf.
Durch hohe Schlagfestigkeit überzeugt auch ABS. ABS ist ein kostengünstiger Kunststoff, der durch niedrige Dichte und gute Formbeständigkeit besticht. Haupteinsatzbereiche sind die Fertigungsindustrie, Elektronikanwendungen und der Fahrzeugbau.
Nylon (PA) ist ein Material, das im Automotive Bereich für stabile mechanische Teile verwendet wird. Es besitzt eine hohe Schmelztemperatur und ist verschleißfest. Außerdem wird es für Anwendungen eingesetzt, die eine gute chemische Beständigkeit und eine hohe Festigkeit erfordern.
Wanddicken
Weitere Design Tipps betreffen die Wanddicken. Generell gilt je dünner die Wände sind, desto weniger Material wird benötigt und desto kürzer wird die Zykluszeit, wodurch Sie Kosten sparen können. Aber die Wände sollten so entworfen werden, dass die gewünschte Festigkeit, Steifigkeit und das Gewicht Ihres Endprodukts beachtet werden.
Für einige Anwendungen reichen dünnere Wände aus. Dünnere Wände verkürzen die Durchlaufzeit und verringern die Kosten Ihrer Bauteile. Meistens reicht eine Wanddicke von 1,5mm-2,5mm aus, aber es gibt auch für jedes Material Empfehlungen für die minimale Wanddicke.
Um Schäden bei den Bauteilen zu vermeiden, sollten die Wanddicken so einheitlich wie möglich gehalten werden. Denn ungleichmäßige Wanddicken und Querschnitte können zu Rissen führen. Außerdem können sie dazu führen, dass das Material ungleichmäßig abkühlt. Dadurch schrumpft das Material und Lunkerbildungen entstehen.
Wenn verschiedene Wanddicken unvermeidbar sind, sollte der Unterschied der Dicke nicht mehr als 15 % der nominalen Dicke betragen. Ein Hilfsmittel zur Ermittlung der Dicke ist die Heuversche Kreismethode. Dabei sollte das Verhältnis jeweils benachbarter Kreisquerschnitte nahe bei eins liegen.
Zusätzlich werden gleichmäßige Übergänge zwischen dünnen und dicken Wänden empfohlen. Dünne Teilbereiche kühlen schneller ab als dicke, nachdem sie aus der Spritzgussform ausgeworfen wurden. Durch plötzliche Übergänge können Einfallstellen und Verformungen entstehen.
Radien
Eines der wichtigsten Spritzguss Design Hinweise ist die Berücksichtigung von Radien. Mit Radien und Abrundungen können Sie weitere Schäden und Schwachstellen an Ihren Teilen verhindern.
Mit Radien und Abrundungen lassen sich Teile leichter ausstoßen. Denn abgerundete Ecken bleiben beim Ausstoßen weniger wahrscheinlich stecken als scharfe Ecken.
Durch scharfe Ecken entstehen Spannungskonzentrationen, die zu Schwächen und Rissen in Teilen führen, da das geschmolzene Metall dafür gemacht ist durch Ecken oder in die Ecken zu fließen. Radien helfen, die Spannung an den Ecken zu glätten. Bei größeren Beanspruchungen einer Stelle sollte auch ein größerer Radius gewählt werden.
Außerdem kann die Herstellung von Teilen mit scharfen Ecken teuer für Sie werden. Denn ein Werkzeug mit scharfen Ecken ist nur mit speziellen Werkzeugen herstellbar. Scharfe Ecken sind meisten nur bei Trennflächen unvermeidbar.
Für die Größe der Abrundungen sollte auch die Wanddicke der Teile berücksichtigt werden. Um Werkstoffanhäufungen bei Übergängen zwischen Wanddicken zu vermeiden, sollten die Abrundungen bestimmte Abmessungen erfüllen. Bei Übergängen zwischen gleichen Wanddicken sollten andere Abmessungen erfüllt werden, als bei Übergängen zwischen unterschiedlichen Wanddicken.

Verwenden Sie Abrundungen anstatt scharfen Ecken, um Schwächen und Risse vorzubeugen.
Rippen
Ein weiterer Spritzguss Design Tipp: Nutzen Sie Rippen um Ihre Teile zu stärken! Rippen und Keile reduzieren den Materialverbrauch und verhindern Verzüge, Senken und Lücken.
Rippen sind essenziell für strukturelle Komponenten. Es ist ratsam sie hinzuzufügen, anstatt die Wanddicke zu erhöhen. So können Sie Material sparen.
Bei der Teilegestaltung sollten Sie die Abmessungen der Rippen beachten. Zur Herabsetzung der Gussspannung Ihrer Teile sollten die Rippen dünner als die Wanddicke sein. Die Dicke der Rippen hängt von der Beanspruchung an der entsprechenden Stelle ab. Aber sie sollte maximal das 0,8-fache der Wanddicke betragen.
Außerdem ist bei beiderseits angeordneten Rippen ein Versatz erforderlich, um Materialanhäufungen und dadurch Lunkerbildung zu verhindern. Es ist besser Rippen versetzt einzusetzen, als auf einen Punkt zentriert.
Kerne
Wenn Rippen und Wände aufeinander treffen müssen, können Kerne nützlich sein. An diesen Stellen können sich Materialanhäufungen bilden und zu Lunkern führen. Kerne können an diesen Knotenpunkten Materialanhäufungen vermeiden.
Allerdings sind Kerne teuer und können das Einformen erschweren. Deshalb sollten sie nach Möglichkeit vermieden und offene Querschnitte angestrebt werden.
Komplizierte Gussstücke erfordern mehrere Teilungsebenen oder zusätzliche Kerne. Durch eine bessere Gestaltung können Sie Teilungsebenen und Kerne einsparen.
Sind Kerne notwendig, sollten sie möglichst einfach gestaltet werden. Damit halten Sie den Aufwand der Kernherstellung gering und verbessern die Wirtschaftlichkeit des Prozesses.
Kerne sollten außerdem sorgfältig gelagert werden, weil sie durch das flüssige Metall einen großen Auftrieb erhalten. Achten Sie dabei auf eine zweiseitige Kernlagerung. Denn bei einer einseitigen Kernlagerung tragen die Kernstützen zur Bildung von Poren und Fehlstellen bei.
Formschrägen
Um weitere Schäden bei der Teileherstellung vorzubeugen, gibt es einige Spritzguss Design Hinweise bei der gießgerechten Gestaltung Ihrer Teile. An verschiedenen Stellen des Gießverfahrens kann es zu Schäden oder Problemen kommen. Zum Beispiel bei dem Ausheben Ihrer Teile.
Teile können beim Ausheben stecken bleiben und so beschädigt werden. Sie sollten deshalb Aushebeschrägen an den Außenflächen des Modells vorsehen, da der Aushebevorgang sonst nicht ohne Beschädigung erfolgen kann. Mit Aushebeschrägen können Sie so Schäden vorbeugen.
Bei Ihren Teilen sollten Sie auch Querrippen und Augen so gestalten, dass sich die Modelle leicht aus der Form heben lassen. Vermeiden Sie dabei Hinterschneidungen, diese können nämlich Ansteckteile erfordern.


Hinterschneidungen
Hinterschneidungen und Trennlinien sind wichtige Aspekte beim Spritzguss Design und haben großen Einfluss auf die Produktionskosten.
Vermeiden Sie Hinterschneidungen möglichst. Mit einfach designten Gussformen mit geradem Rückzug lassen sich keine Teile mit Hinterschneidungen herstellen. Denn das Teil bleibt dann beim Auswurf stecken. Hinterschneidungen sind ausschließlich durch Ändern der Formteilung oder verschiebbare Kerne in der Form möglich. Diese treiben die Werkzeugkosten aber erheblich in die Höhe.
Die Änderung der Formteilung bzw. die Verschiebung der Trennlinie ist vor allem für Hinterschneidungen an der Außenseite des Gussteils ein geeignetes Mittel.
An der Trennlinie laufen beide Hälften der Gussform zusammen. Da die Trennlinie eine sichtbare Naht (einen Gussgrat) auf dem Endprodukt hinterlässt, sollten sie beim Entwurf Ihres Produkts berücksichtigt werden. Platzieren Sie sie also am besten dort, wo sie am wenigsten sichtbar ist. Der Gussgrat kann zwar nach dem Guss durch Nachbearbeitung entfernt werden. Das ist aber mit zusätzlichen Kosten im Fertigungsprozess verbunden.

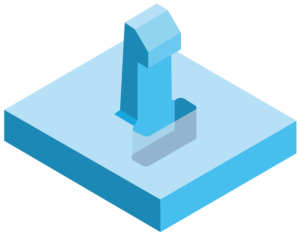
Schraubdome
Für Einsätze, Anbauteilstifte oder selbst schneidende Schrauben eignen sich Schraubdome. Schraubdome sind zylinderförmige Abstandshalter, die in das Kunststoffteil gegossen werden.
Dome sollten nicht freistehen, sondern immer mit einer Rippe an einer Seitenwand oder einer Eckversteifung am Boden befestigt werden. Um sichtbare Einfallstellen an der Außenseite zu vermeiden, sollte die Stärke dabei nicht 60% der Gesamtstärke überschreiten. Zum Beispiel sollten bei einer Außenwandstärke von 3 mm die Rippen nicht dicker als 1,7mm sein.
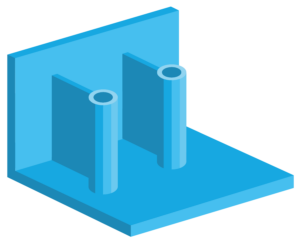
Angussöffnungen
Essenzielle Spritzguss Design Hinweise für die Teilegestaltung betreffen die Lage der Angussöffnungen. Durch Angussöffnungen gelangt geschmolzenes Material in die Form. Deshalb muss die Lage und Art der Öffnung gut überlegt sein, damit es nicht zu Qualitätsverlusten kommt.
Am häufigsten werden Filmangüsse verwendet. Filmangüsse bieten sehr gute Verarbeitungsmöglichkeiten und können, wenn nötig, vergrößert werden. Da ein Filmanguss vom Angusskanal aus verjüngt ist, befindet sich der kleinste Punkt an der Teileoberfläche. Deswegen liegt der Erstarrungspunkt zwischen dem Teil und dem Angusskanal, wodurch an der Oberfläche des Teils keine Hitze entsteht. Nachdem der Filmanguss manuell entfernt wurde, bleibt ein Angussrest von 0,13 mm.
Beim Tunnelanguss wird ein Anguss seitlich in das Teil oder in einen Stabanguss platziert. Der Zugang zum Teil wird bei Tunnelangüssen von außen angelegt, allerdings bleiben die Angussreste in der Regel gering, da sie sich auf halber Strecke unter der Teileoberfläche befinden. Bei Stabangüssen müssen Sie aber aufpassen, da aufgrund von Hitze oder Teiledicke ein unschöner Schatten an der gegenüberliegenden Seite des Teils zurückbleiben kann. Dieser Angusstyp sollte daher vorsichtig verwendet werden bei äußerlichen Teilen.
Hot-Tip Gates werden empfohlen, da die Angüsse kleine Abfallmengen verursachen. Am besten eignen sich Hot-Tip Gates für Teile, die von der Mitte zu den Außenkanten gleichmäßig gefüllt werden müssen. Dadurch wird eine Formverschiebung reduziert, da bei Filmangüssen ein unausgewogener Druck in einer Form entstehen kann. Hot Tip Gates sind häufig optisch die beste Lösung, da die Durchmesser etwa 1,3 mm betragen und in einem Logo oder einer Beschriftung versteckt werden können.
Am wenigsten optisch ansprechend sind direkte Kegelangüsse. Diese haben einen großen, schwer entfernbaren Durchmesser und benötigen oft eine Vorrichtung, die durch Fräsen entfernt wird. Direkte Kegelangüsse werden bei Werkstoffen verwendet, die einen hohen Glasgehalt besitzen oder bei Teilen, deren Mitte eine Nachbearbeitung erfordert.
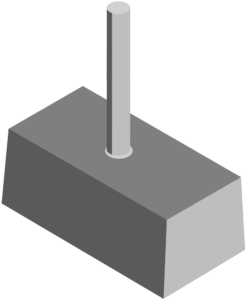
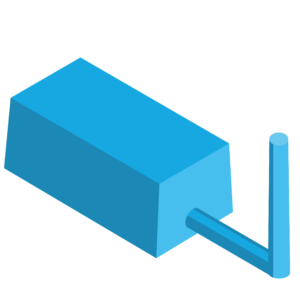
Verwenden Sie anstatt direkten Kegelangüssen andere Angussarten wie den Filmanguss.